Bevel Gears
Bevel gears are specialized gears designed to transmit power between intersecting shafts, typically at a 90-degree angle, though other angles are possible. They have conical shapes with teeth cut along the angled surface, allowing smooth and efficient torque transfer. Bevel gears come in various types, including straight, spiral, and hypoid, each suited for specific applications. Straight bevel gears have straight teeth and are simpler but noisier, while spiral bevel gears have curved teeth for quieter, smoother operation. They’re widely used in automotive differentials, machinery, and robotics for precise power transmission.
Types of Bevel Gears for Sale
What Is a Bevel Gear?
Bevel gears come in different types, including straight bevel gears, spiral bevel gears, and hypoid gears. Straight bevel gears have straight teeth and are simpler in design, typically used in applications with lower speeds and loads. Spiral bevel gears have curved teeth set at an angle, which allows for smoother and quieter operation at higher speeds. Hypoid gears, a variation of bevel gears, are used when the axes of the shafts are offset rather than intersecting.
The material composition of bevel gears varies depending on their application. They can be made from steel, brass, stainless steel, or even advanced polymers like polyacetal resin or polyketone resin. Each material provides specific benefits such as strength, corrosion resistance, or lightweight properties.
Bevel gears are widely used in industries such as automotive, aerospace, industrial machinery, and robotics. Common examples include their use in differentials in cars, enabling wheels to rotate at different speeds, and in power tools, where they help transfer motion efficiently between angular shafts.
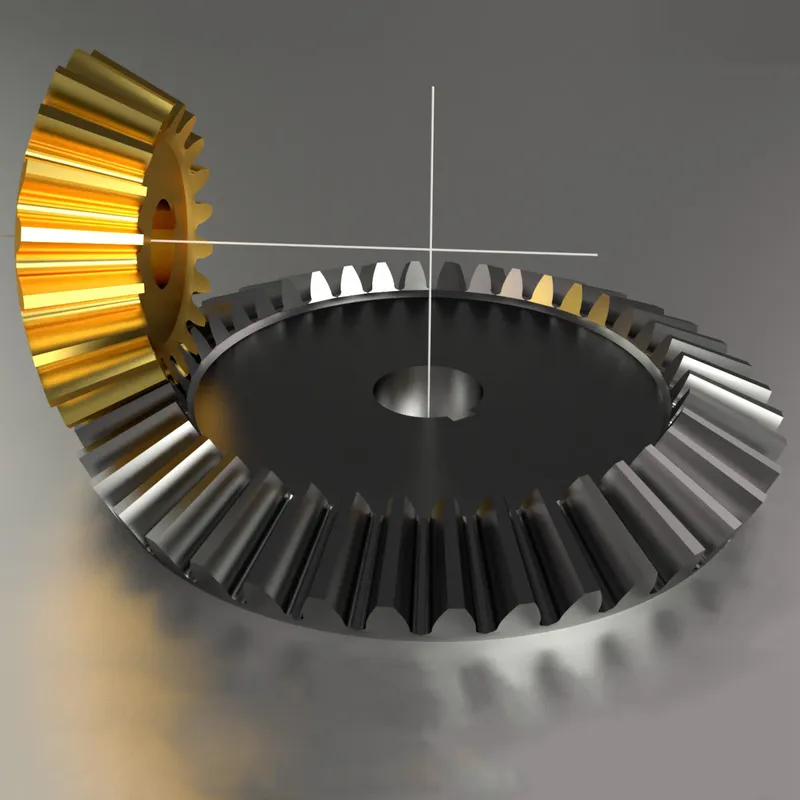
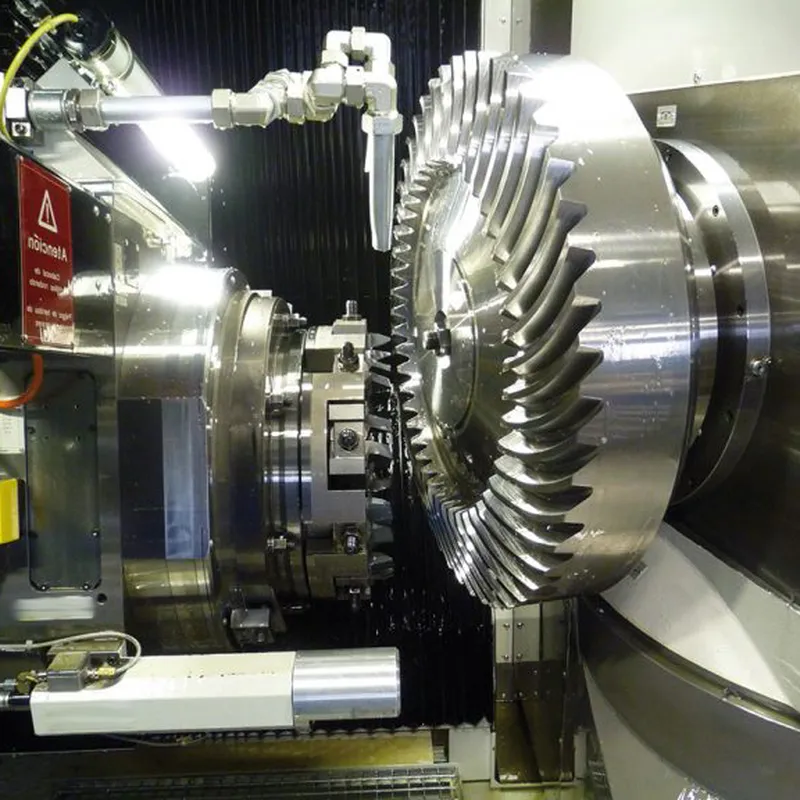
Common Different Types of Bevel Gears
Straight Bevel Gear
Straight bevel gear, with a 43% market share, is the largest product category of bevel gear. A straight bevel gear is a type of bevel gear where the teeth are cut straight and taper off towards the apex of the gear. Since the force acting in the axial direction is small, it is often used in places where thrust loads are averse.
It also has the advantage of simplifying the bearing. The disadvantage is that when rotating at high speeds, the noise and vibration increase. Because of these features, straight bevel gears are recommended when cost is a priority, high-speed rotation is not required, and noise is not a problem.
Generally used when operating at a relatively low speed (circumferential speed of 2m/s or less). It is relatively easy to manufacture and is especially suitable for machine tools, printing machines, etc., as well as differential devices—the most popular bevel gear for power transmission.
Spiral Bevel Gear
Spiral bevel gear is another type of bevel gear. The tooth traces are spiral and helical, creating a helical angle, and the two intersecting gears intertwine with each other, creating a stronger mesh. The advantages include low noise and vibration even during high-speed rotation, high tooth surface strength, and less stress on the tooth surface.
In addition, it has a curved tooth trace (typically an arc) on the pitch cone, allowing for smoother operation than straight bevel gears. This is mainly used for high-speed operation with a pitch circumferential speed of 10 m/s or more.
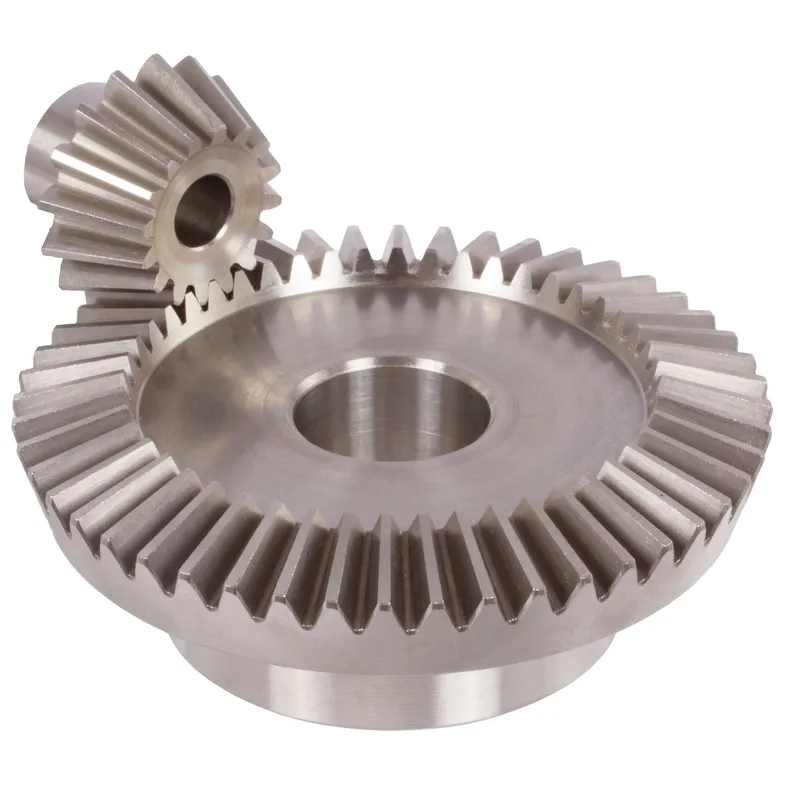
Straight Bevel Gear
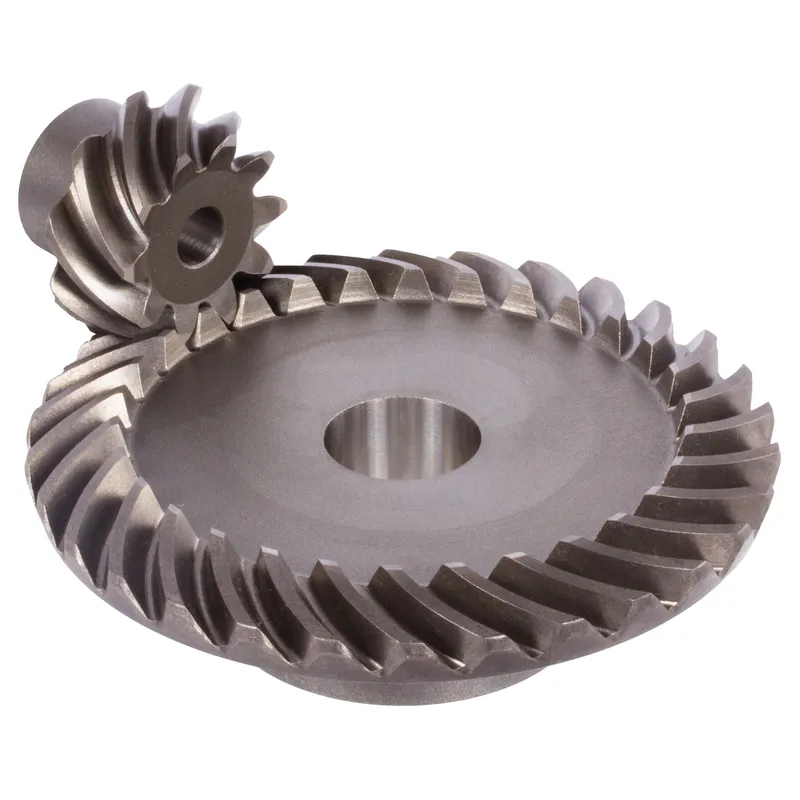
Spiral Bevel Gear
Zerol Bevel Gear
A spiral bevel gear with a helix angle of 0 degrees is also called a zero bevel gear. It is a bevel gear that has the characteristics of straight bevel gears and spiral bevel gears with the same force applied to the teeth.
Compared to spiral bevel gears, the major advantage is that the thrust load can be suppressed. It is used in industrial equipment and automobiles. The tooth traces are curved and have a very beautiful appearance. But unlike the tooth profile of a spiral bevel gear, it does not have a tooth profile in which the teeth are twisted together in a conical shape on the outer periphery.
Hypoid Bevel Gear
A hypoid gear has spiral tooth traces and staggered shafts that are neither parallel nor intersecting on the input or output sides of the gear. Although similar to spiral bevel gears, they differ in that their axes intersect.
Both are similar in that they utilize a large reduction ratio and are used with large torque. These gears are mainly used in automobile drive systems, train drive systems, speed reducers (buses, trucks, luxury private cars), etc.
The advantages of hypoid gears include a large reduction ratio, low noise and vibration, and strength that can withstand large torque. Regarding the reduction ratio, hypoid gears can increase the number of teeth on the input side (hypoid pinion) and the output side (hypoid gear).
Miter Bevel Gear
Miter gears with the same number of teeth are called miter gears. The standard shaft angle is 90 degrees, and the pitch plane is 45 degrees. There are also 45-degree, 60-degree, and 120-degree miter gears, and miter has the meaning of miter or joint. These are the power transmitting, driving, and transporting parts of equipment.
Power can be transmitted through orthogonal axes. It is often used in applications where there is no need to change gears, just by changing the direction of rotation of a shaft.
Miter gear is mainly suitable for use in the semiconductor industry, the food industry, general industrial machinery, and agricultural machinery.
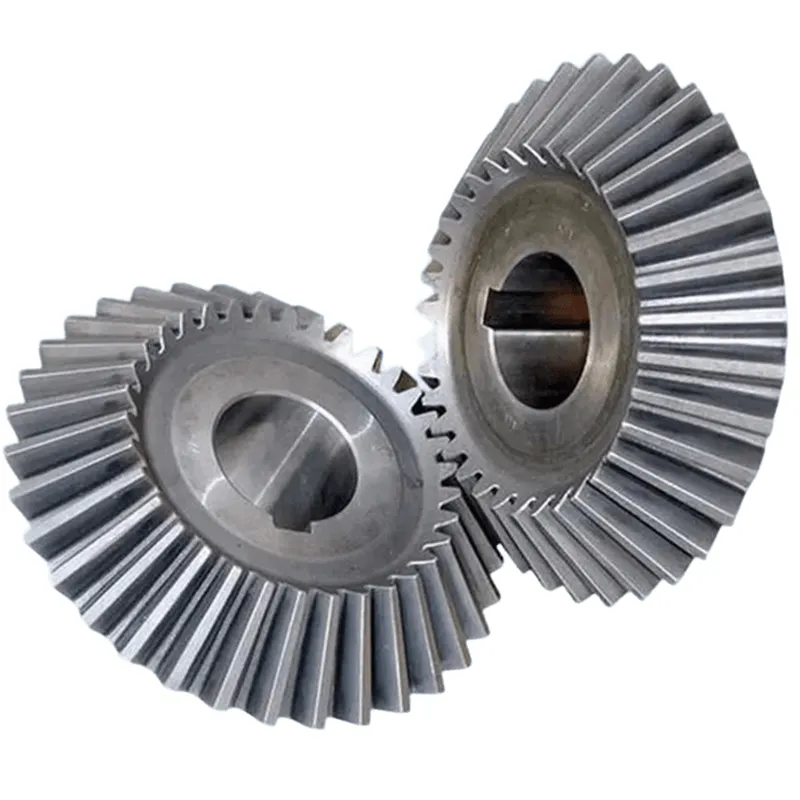
Zerol Bevel Gear
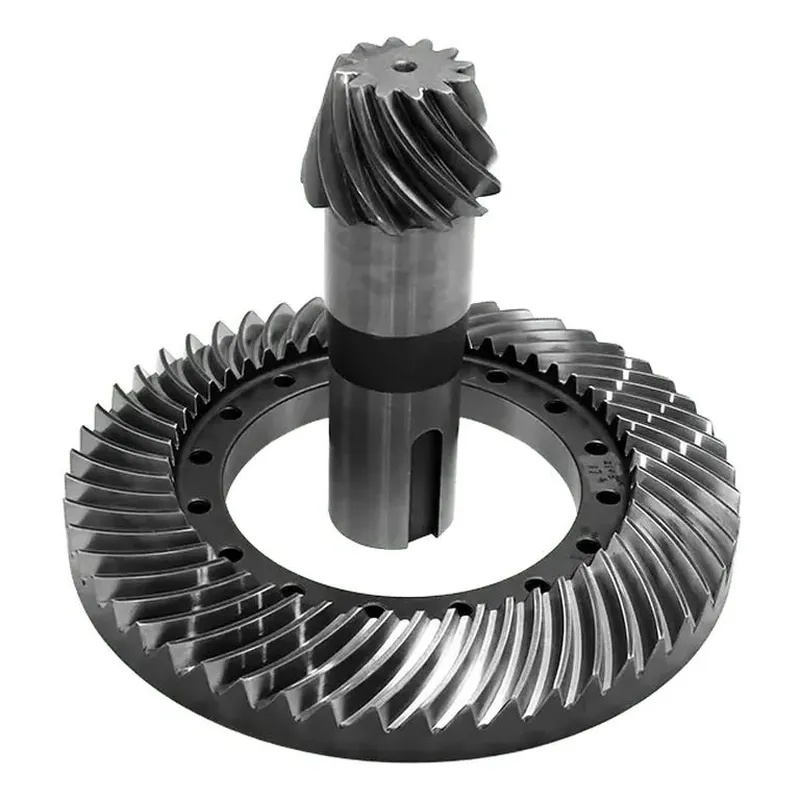
Hypoid Bevel Gear
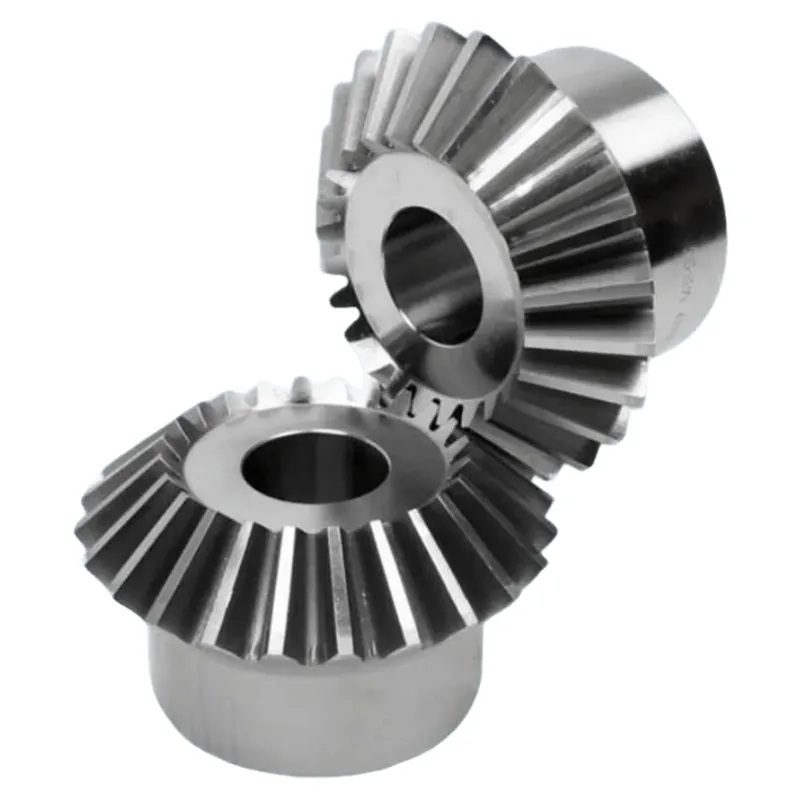
Miter Bevel Gear
Straight Bevel Gear vs. Spiral Bevel Gear
Feature | Straight Bevel Gear | Spiral Bevel Gear |
Tooth Profile | Straight teeth cut along the cone axis | Helical teeth with a curved profile |
Noise Level | Noisier due to tooth impact at engagement | Quieter due to gradual tooth engagement |
Vibration | Higher vibration due to impact | Lower vibration due to smoother meshing |
Thrust Load | Low axial thrust load | Higher axial thrust load due to helical angle |
Efficiency | Lower efficiency at high speeds | Higher efficiency at high speeds |
Applications | – Low-speed applications – Cost-sensitive applications – Applications where noise is not a major concern | – High-speed applications – Applications requiring smooth operation – Applications where noise reduction is important |
Manufacturing Complexity | Simpler to manufacture | More complex to manufacture |
Cost | Generally lower cost | Generally higher cost |
Miter Gear Vs Bevel Gear
![]() | ![]() |
Miter Gear | Bevel Gear |
Bevel Gear Advantages and Disadvantages
Advantages of Bevel Gears
(1) Versatile Shaft Angles
One of the primary advantages of bevel gears is their ability to transmit power between shafts at various angles, not just limited to 90 degrees like miter gears.
(2) Smooth and Quiet Operation
Spiral bevel gears and hypoid bevel gears offer smoother and quieter operation compared to straight bevel gears. The curved teeth of spiral bevel gears provide a more gradual engagement, reducing vibration and noise.
(3) High Torque Capacity
Bevel gears, particularly hypoid bevel gears, are capable of transmitting high torque loads. The offset pinion axis in hypoid gears allows for larger tooth contact areas, increasing their load-carrying capacity.
Disadvantages of Bevel Gears
(1) Complex Manufacturing
The manufacturing process for bevel gears, especially spiral and hypoid bevel gears, is more complex and costly compared to other gear types. Due to the sliding action between the teeth, bevel gears are subject to higher friction compared to spur or helical gears.
(2) Potential for Backlash
Bevel gears may experience backlash, which is the clearance or play between mating gear teeth. Backlash can result in reduced positional accuracy and increased wear, particularly in applications requiring precise positioning or low-speed operation.
(3) Limited Speed Ratios
While bevel gears offer versatility in shaft angles, they are limited in terms of achievable speed ratios compared to other gear types like worm gears.
Bevel Gear Examples and Applications
Bevel gears, characterized by their conical shape and intersecting shafts, are vital components in various mechanical systems. Their versatility enables diverse applications, such as changing the direction of rotation by 90 degrees and transmitting power. Here are several usages and applications of bevel gears:
Automotive
Bevel gears are extensively utilized in automotive applications such as differential drives, transmission systems, and rear-wheel drive systems in automobiles. That enables wheels to rotate at varying speeds while maintaining traction and stability, especially during turns. Among its products, straight bevel gear is the largest segment, in which automotive has a 53% share.
Light and Heavy Equipment
Bevel gears are used for propulsion or running auxiliary units in light and heavy equipment like lawnmowers, small tractors, cement mills, cone crushers, sand mixers, forklifts, and mining machinery.
They are essential to the transmission of power by enabling the efficient transfer of rotational motion from the engine to the wheels or cutting blades.
Railroad Drives
Bevel gears are also utilized in the gearboxes and differentials of rail vehicles, enabling the locomotive to move forward or backward. They ensure smooth operation and efficient power distribution.
Construction Equipment
They are commonly employed in the driveshafts of construction vehicles such as excavators, loaders, and bulldozers. The bevel gears in construction equipment provide reliable torque transmission for lifting and positioning heavy loads with precision and control.
Industrial Gearbox
Bevel gears are employed in conveyor systems, elevators, and material handling equipment, ensuring efficient movement and transfer of goods within industrial facilities.
Special Applications
Bevel gears are used in coffee grinders with large hand-cranked handles, hand-cranked hand mixers and hand drills, and radio-controlled devices. These are also essential for aircraft engines, the marine industry, and the medical field for optimal performance and safety.
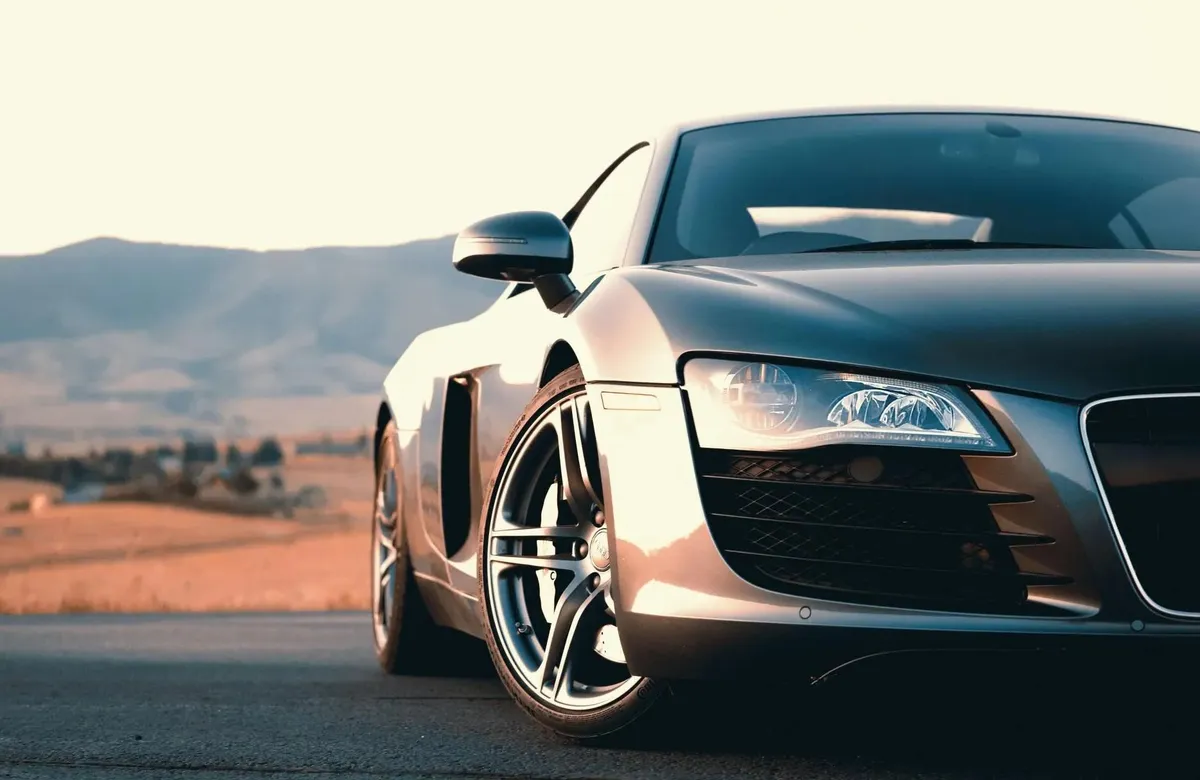
Bevel Gear for Automotive
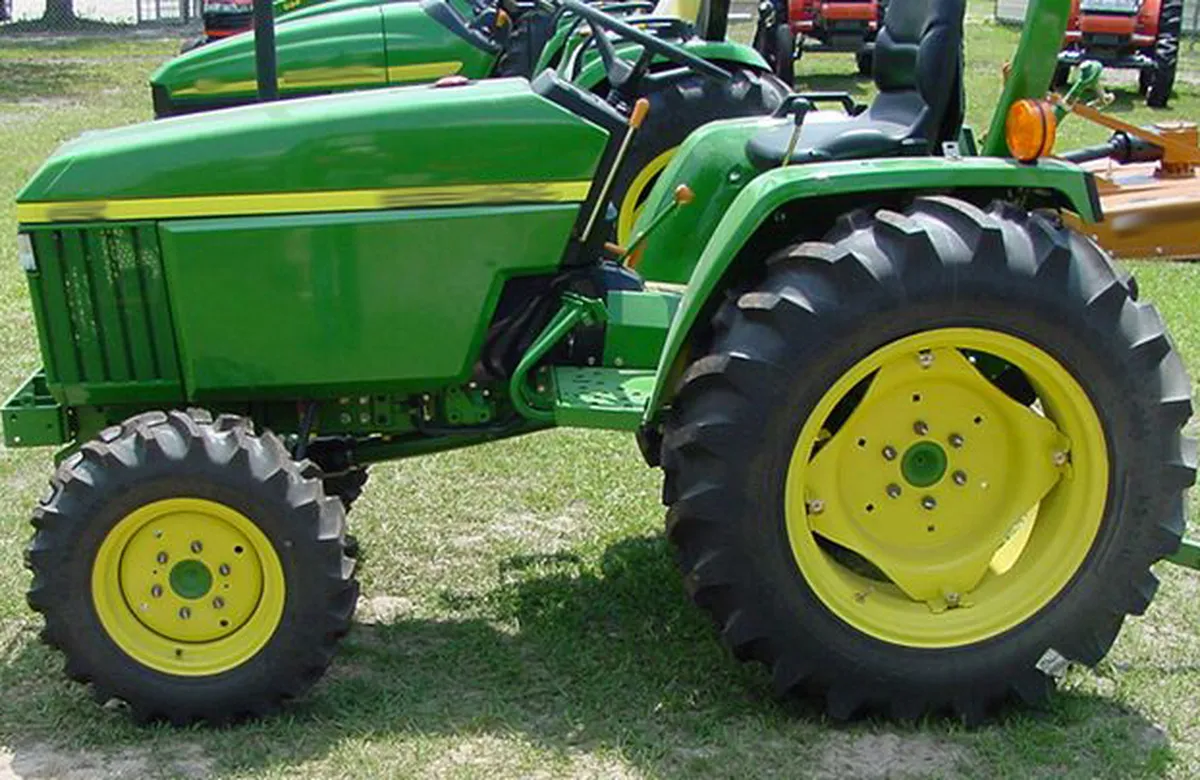
Bevel Gear for Small Tractors
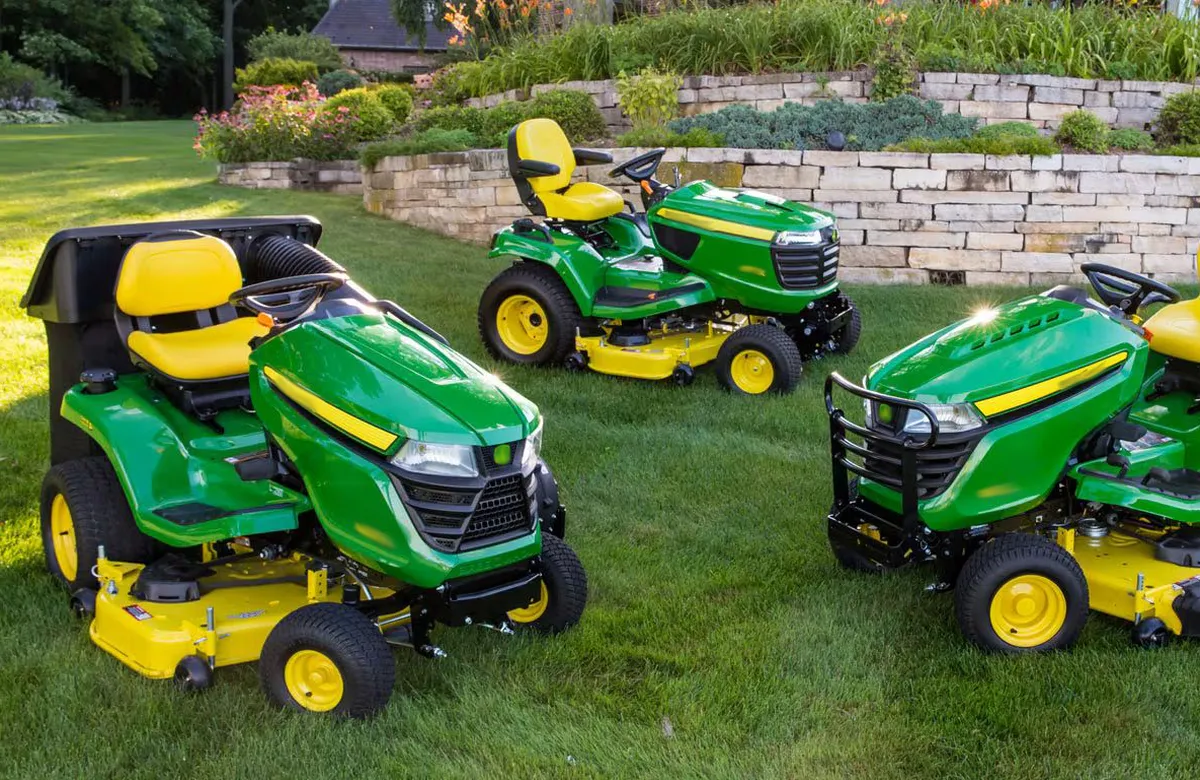
Bevel Gear for Lawnmowers
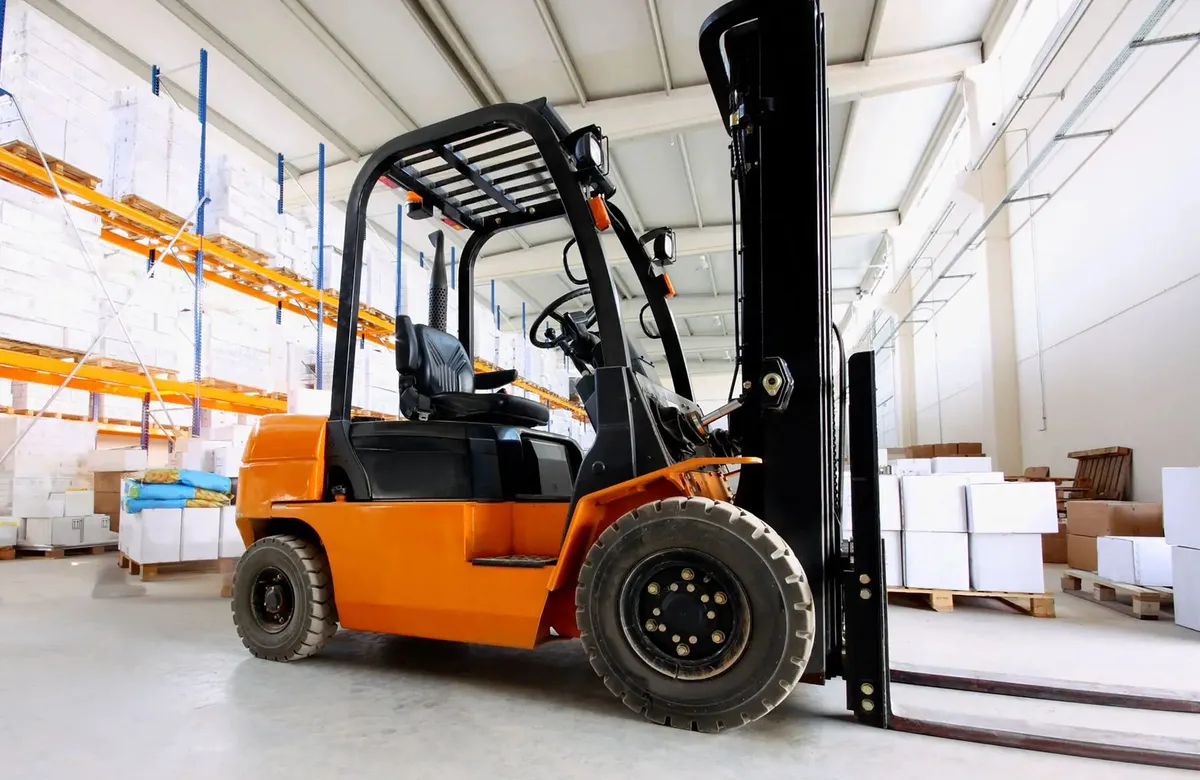
Bevel Gear for Forklifts
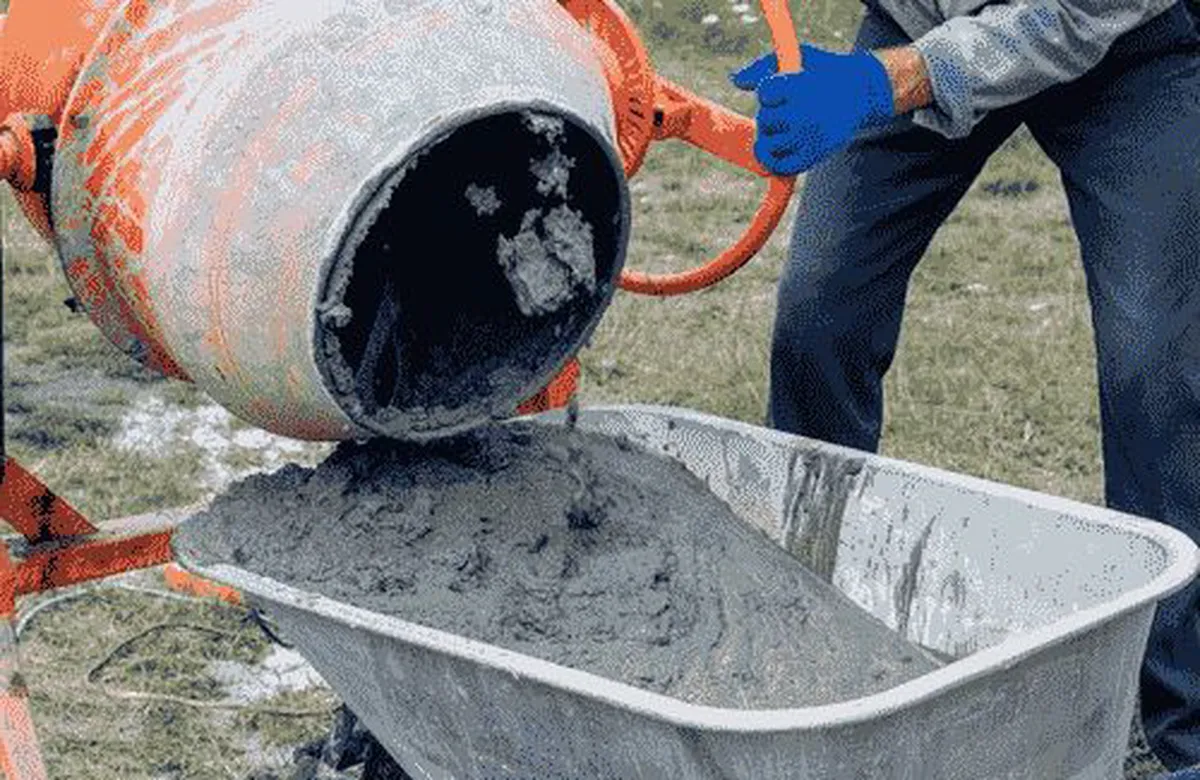
Bevel Gear for Sand Mixers
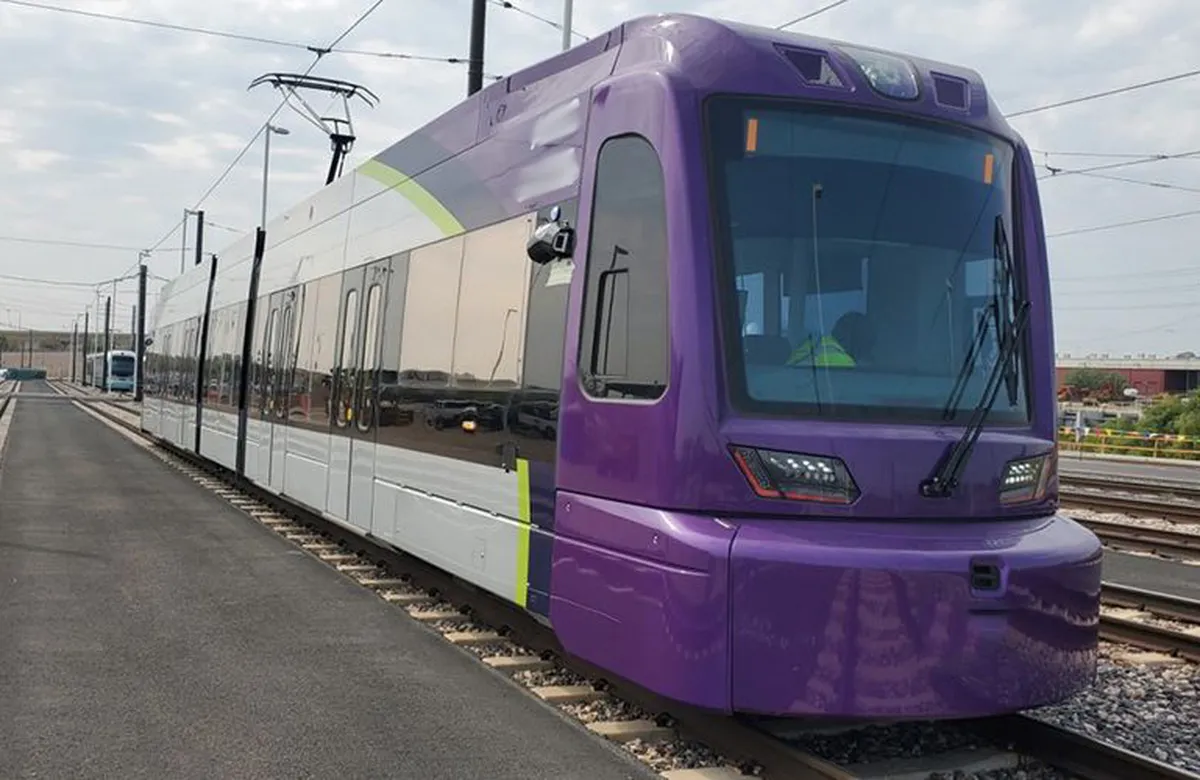
Bevel Gear for Rail Vehicles
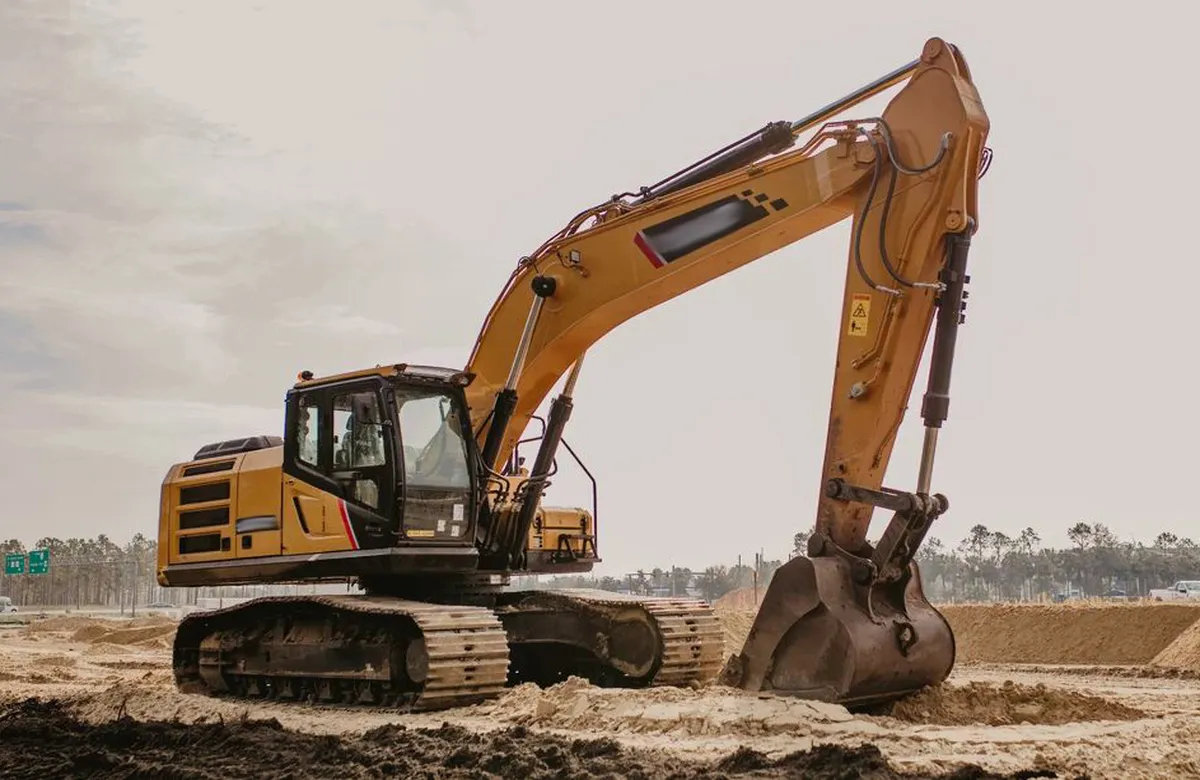
Bevel Gear for Excavators
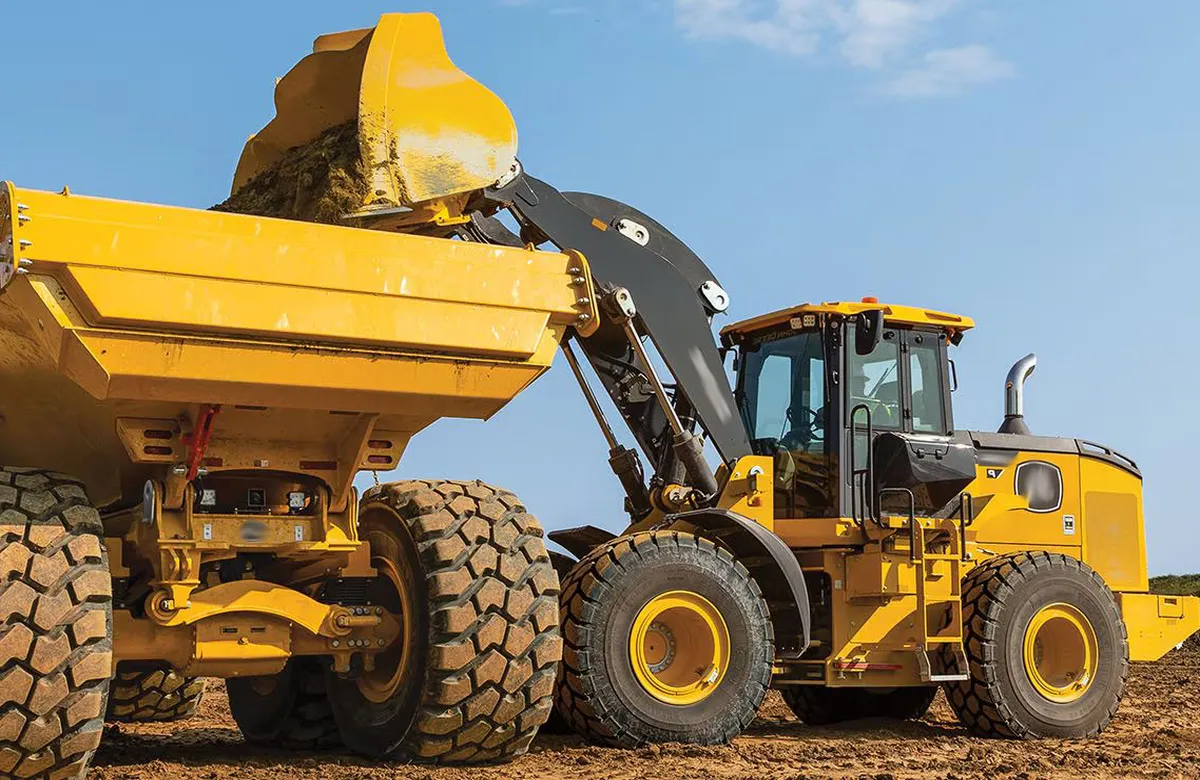
Bevel Gear for Loaders
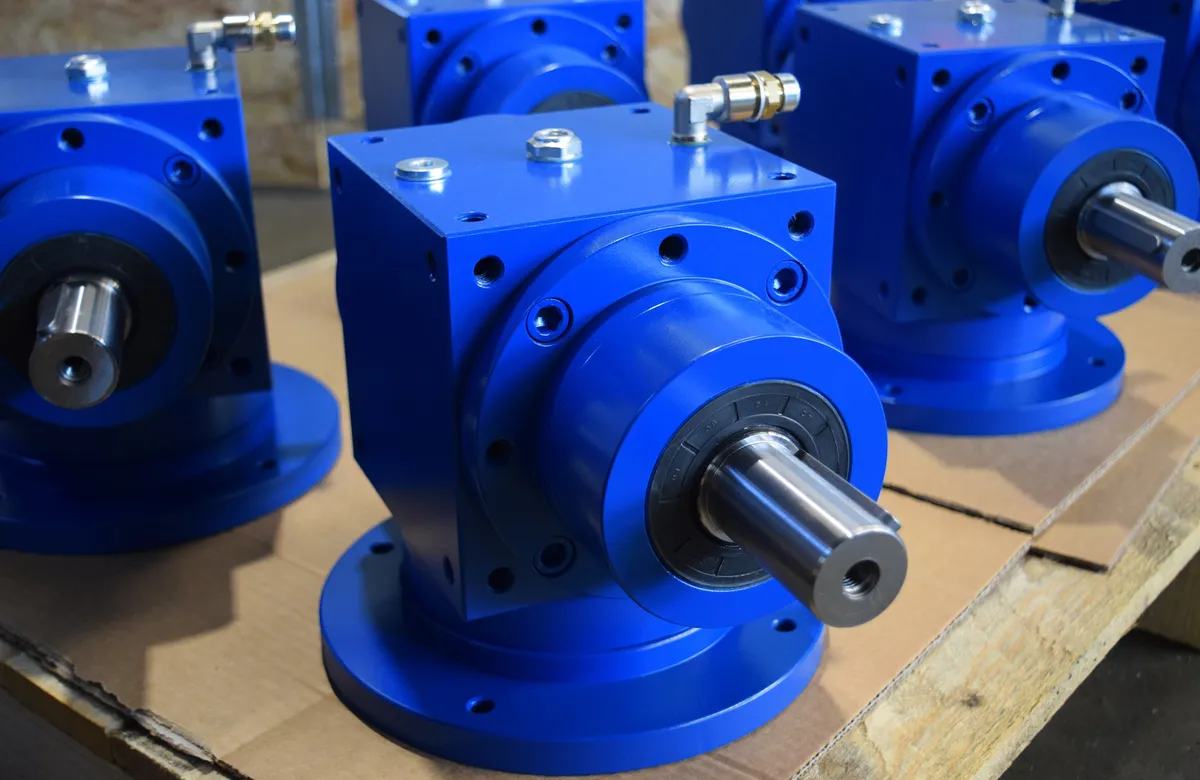
Bevel Gear for Industrial Gearbox
Why Choose CMN’s Forged Bevel Gears?
CMN CMN Transmission stands out as a trusted and leading forged bevel gear manufacturer and supplier, providing a comprehensive range of premium-quality forged bevel gear products designed to cater to diverse industrial applications. Our commitment to excellence is underpinned by stringent certifications, advanced research capabilities, and a strong focus on innovation.
1. Certification and Standards:
CMN operates under the highest quality and safety standards, ensuring unparalleled reliability in our products. We hold the IATF16949:2016 certification, a globally recognized standard for automotive quality management systems. Additionally, we adhere to Level 3 Safety Production Standardization, guaranteeing optimal production safety practices. Our environmental and occupational health systems are certified under ISO14001:2015 and ISO45001:2008, reflecting our dedication to sustainability and employee welfare.
2. Research and Development Strength:
Innovation drives our success. CMN boasts a professional R&D team of six skilled experts, coupled with a dedicated technology research and development center. This robust foundation allows us to continuously improve our forging techniques and develop cutting-edge gear solutions that meet and exceed client expectations.
3. Patent Achievements:
Our focus on innovation is evident through our impressive portfolio of intellectual property. CMN holds two invention patents and 54 utility model patents, demonstrating our leadership in advanced bevel gear technology. These advancements ensure our products deliver superior performance, durability, and precision.
With CMN, you gain a partner who combines technical expertise, certified quality, and innovation to deliver exceptional bevel gear solutions tailored to your needs.
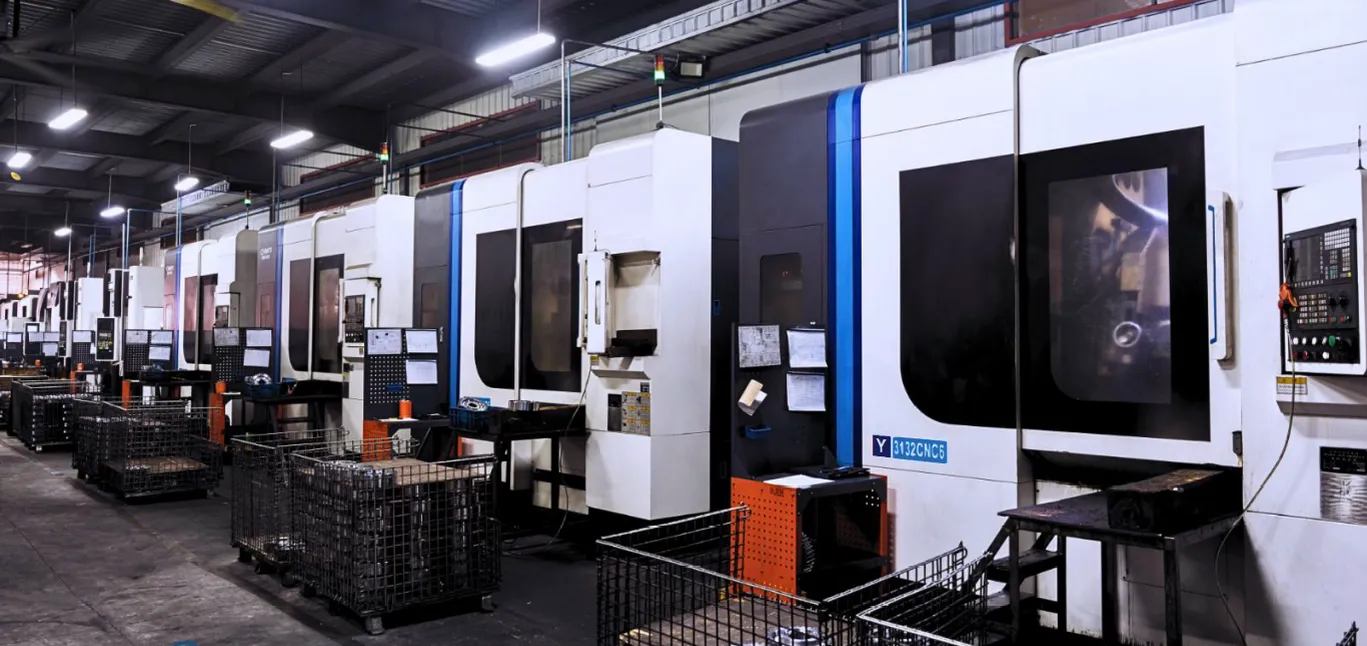
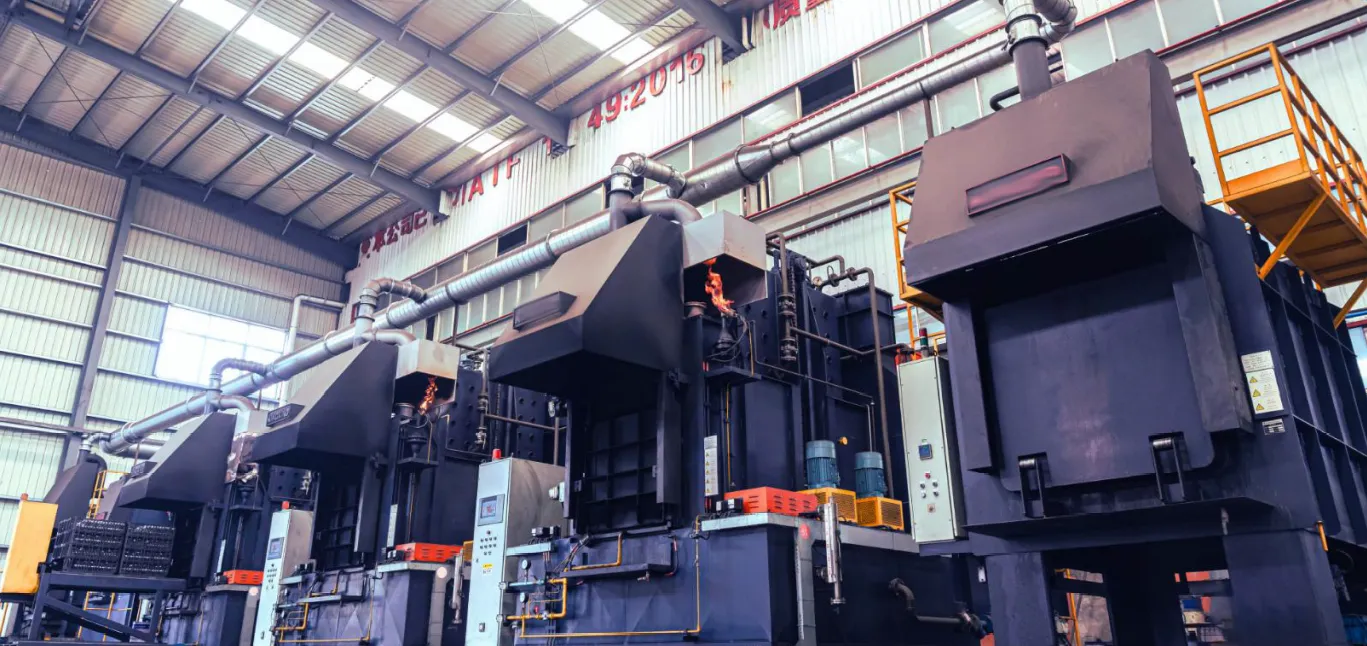
Our Cooperative Brand
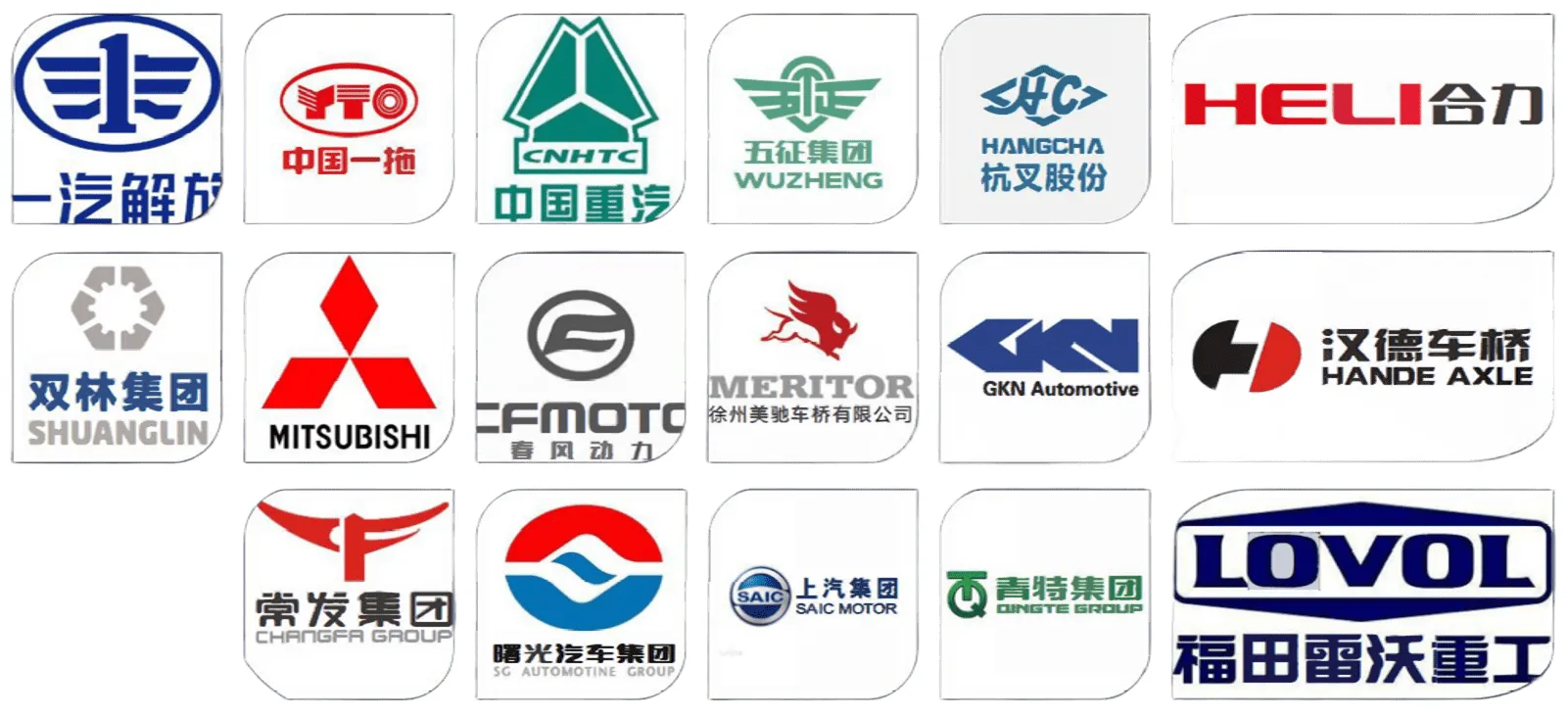
Bevel Gear Manufacturing Process
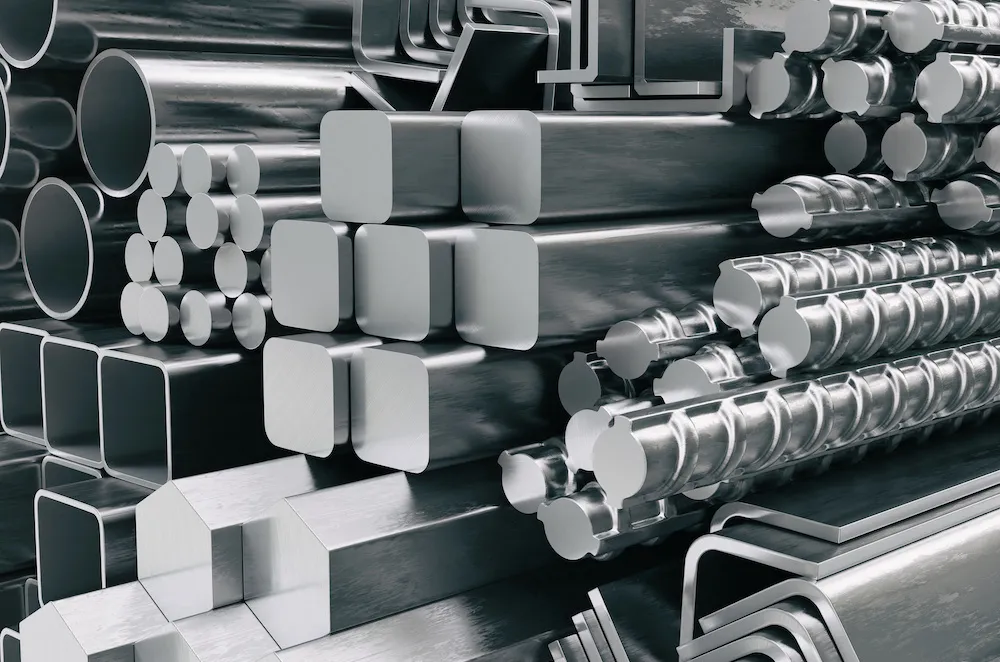
STEP 1: Material Preparation
The appropriate material is selected based on desired gear properties, ensuring optimal strength and durability.
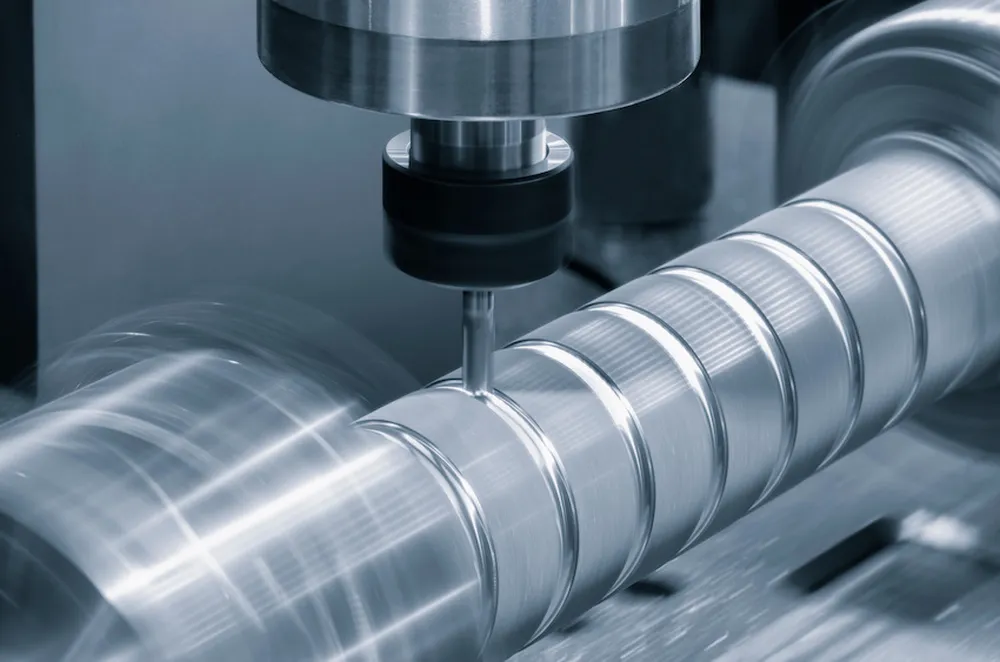
STEP 2: Cutting
The chosen material is cut into manageable sizes, preparing it for subsequent processing.
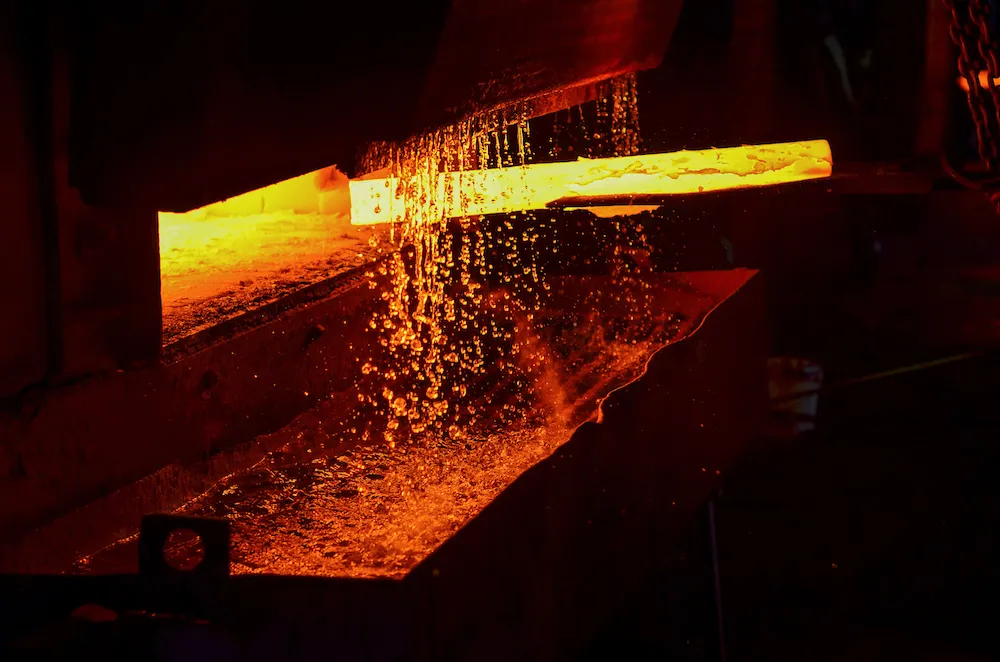
STEP 3: Heat Treatment
The cut pieces undergo heat treatment to enhance their mechanical properties, such as hardness and toughness.
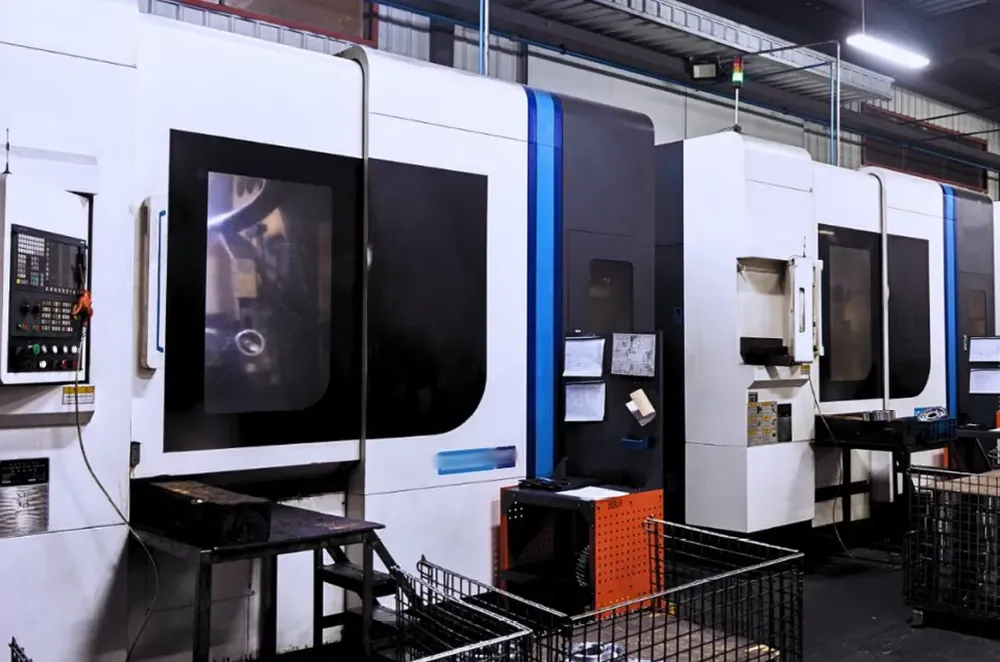
STEP 4: Lathe Machining
The heat-treated pieces are shaped on a lathe, ensuring symmetry and preparing them for detailed machining.
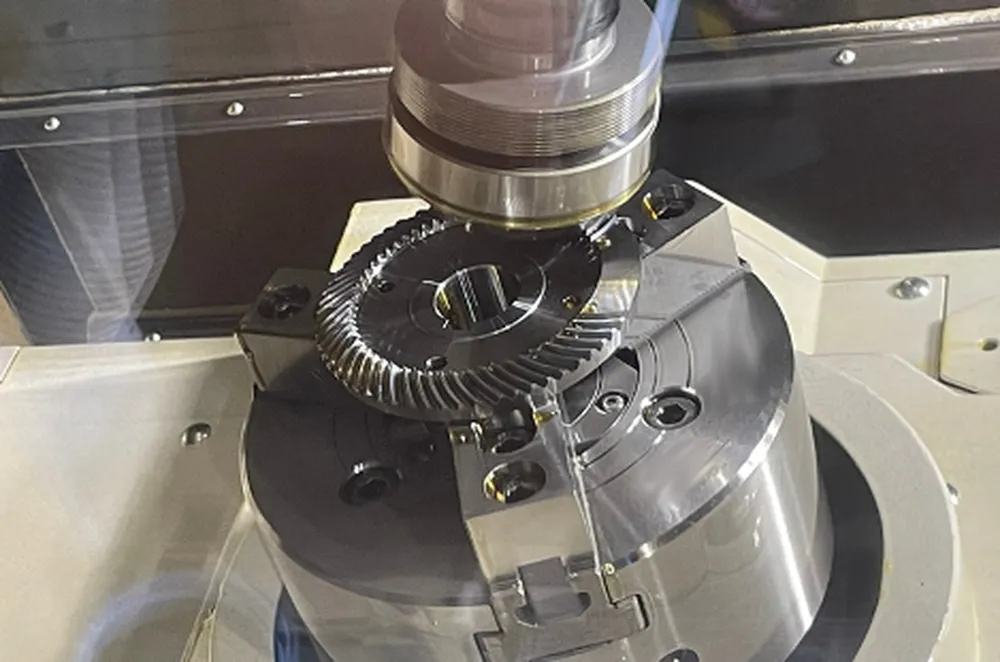
STEP 5: Gear Cutting
The teeth of the gear are formed using specialized gear cutting machines, creating the unique helical shape.
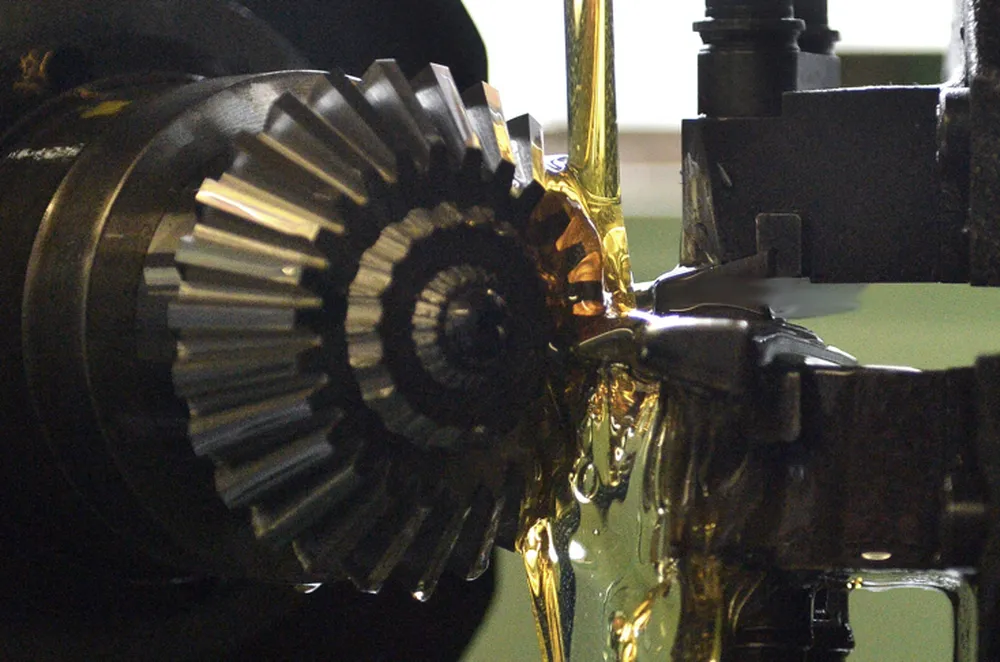
STEP 6: Broaching
Internal features, like keyways or splines, are created using a broaching process, which removes material with a toothed tool.
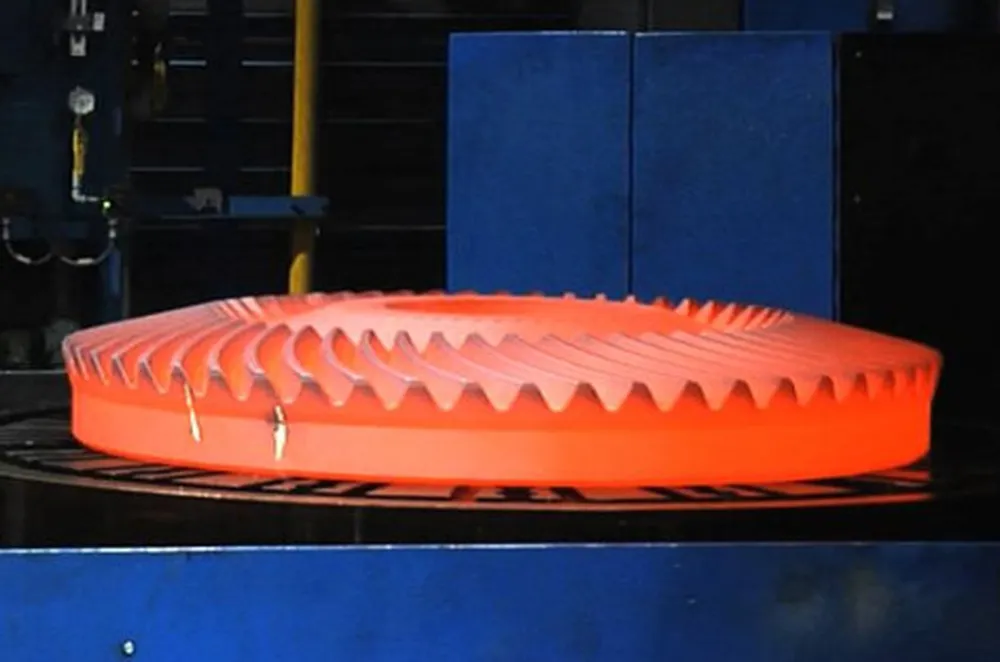
STEP 7: Carburizing with high frequency
The gear undergoes a carburizing process, enriched with carbon, and is then treated with high-frequency heat to harden its surface.
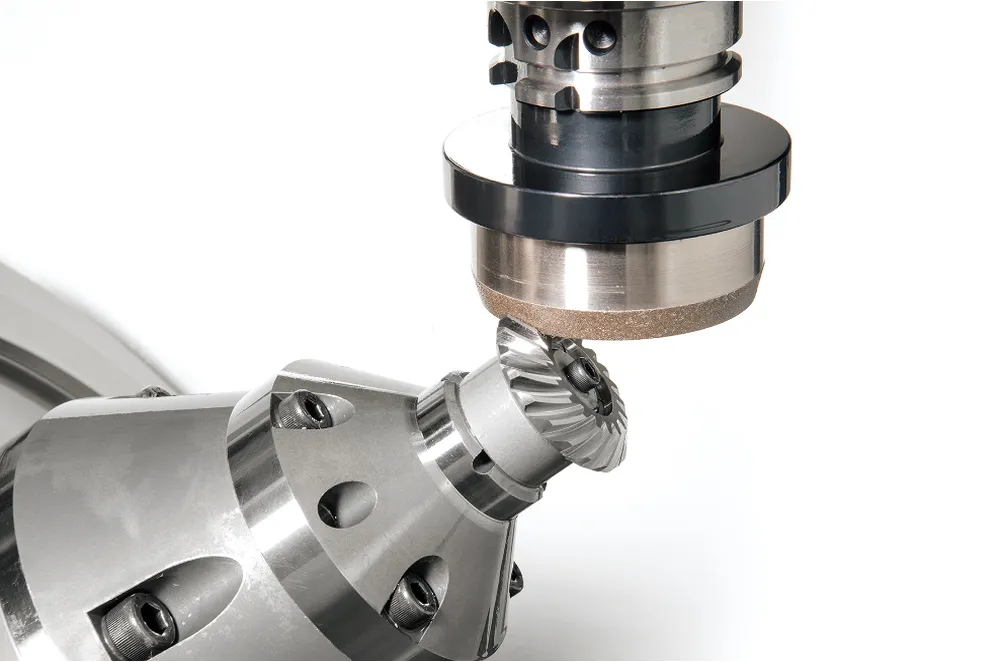
STEP 8: Gear grinding
The gear teeth are finely ground using specialized equipment, ensuring smooth engagement and precise tooth profiles, enhancing the gear’s operational performance./span>

STEP 9: Inspection
The final gear is rigorously inspected for quality and compliance with design specifications. Advanced tools and machines are used to measure dimensions, alignments, and other critical parameters to guarantee optimal performance in real-world applications.
Custom Bevel Gears
As a leading bevel gear manufacturer and supplier, we specialize in delivering premium-quality, custom bevel gear solutions tailored to meet the unique demands of various industries. Whether it’s for automotive, construction, mining, agriculture, or industrial applications, our custom bevel gears are designed for superior performance, durability, and precision. With advanced manufacturing capabilities, we offer a wide range of materials, gear types, and finishes to ensure optimal functionality. Contact us today to share your specific requirements and receive a personalized quotation for your project!
Our Customer Reviews
–Italian Customer
–American Customer
–Korean Customer
–German Customer
–British Customer
–Canadian Customer
–Australian Customer
–Brazilian Customer
–Russian Customer